-
Ammonium Polyphosphate Flame Retardant
-
Intumescent Flame Retardant
-
Halogen Free Flame Retardant
-
Fabric Flame Retardant
-
APP Ammonium Polyphosphate
-
Wood Flame Retardant
-
PP Flame Retardant
-
Additives For Adhesives And Sealants
-
Water Based Fire Retardant
-
Paper Fire Retardant
-
PU Flame Retardant
-
Halogen Free Fire Retardants
-
AP422 CROS484 Equal Type
Hydrophilic Ammonium Polyphosphate Flame Retardant TF-212 for Various Coating Processes
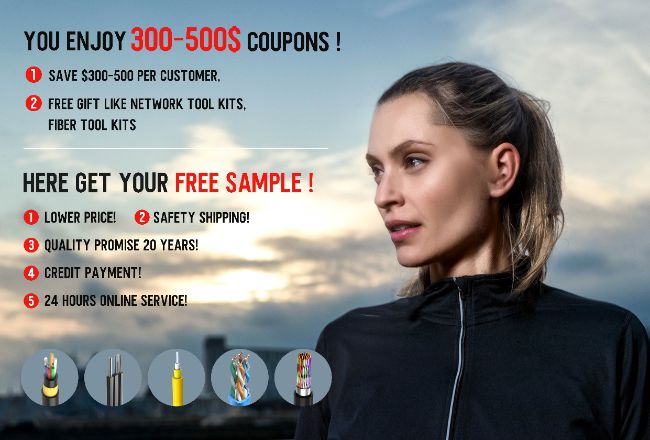
Contact me for free samples and coupons.
Whatsapp:0086 18588475571
Wechat: 0086 18588475571
Skype: sales10@aixton.com
If you have any concern, we provide 24-hour online help.
xExplosive Limit | Non-explosive | Chemical Formula | NH4H2PO4 |
---|---|---|---|
Hydrophilic Or Hydrophobic | Hydrophilic | Product Name | Ammonium Polyphosphate Flame Retardant |
PH | 5.5-7.5 (10% Solution) | Whiteness | >92 |
Appearance | White Powder | Solubility | Insoluble In Water |
Highlight | Ammonium Polyphosphate Flame Retardant TF-212,Hydrophilic Ammonium Polyphosphate Flame Retardant |
Product Description:
The Ammonium Polyphosphate Flame Retardant has a decomposition temperature of over 260°C, which means it can withstand high temperatures without breaking down. This makes it an ideal choice for applications where high heat resistance is required.
The pH of the Ammonium Polyphosphate Flame Retardant is between 5.5-7.5 (10% Solution), which makes it a neutral product. This ensures that it is safe to use in various applications without causing any adverse reactions.
The viscosity of the Ammonium Polyphosphate Flame Retardant is less than 20, which makes it a low-viscosity product. This makes it easy to apply in various applications without causing any issues.
Overall, the Ammonium Polyphosphate Flame Retardant is an excellent product that is widely used in various applications such as Ammonium Polyphosphate Retardant, Ammonium Polyphosphate Flameproofing, and Ammonium Polyphosphate Fireproofing. Its high heat resistance, water resistance, neutral pH, and low viscosity make it an ideal choice for various applications.
Applications:
TF-212 Ammonium Polyphosphate Flame Retarder is also used in the textile industry. It is commonly used in the production of flame-retardant fabrics, such as curtains, bed sheets, and upholstery. It can also be used in the production of outdoor clothing, such as hiking and camping gear, which requires high flame retardancy.
In summary, Ammonium Polyphosphate Flame Retardant is a highly effective product that can be used in a variety of industries. Its ability to inhibit the combustion process and prevent the spread of flames makes it an essential component in the manufacturing of various products. Its hydrophilic nature and insolubility in water make it an ideal choice for applications where high flame retardancy is required.
Different process for textile coating
Calendar Coating
The calendar coating process fuses fabric with solid rubber, transforming them into a composite material. This is achieved by feeding the fabric and rubber through a series of calender rolls. The rollers exert controlled heat and pressure while maintaining precise speed parameters to ensure a consistent and strong bond. The result is a coated fabric with enhanced properties suitable for diverse industrial applications.
Film Lamination
Our film lamination process meticulously combines fabric with a polymer film, creating a composite material with superior properties. The fabric and film are pressed together under precise mechanical pressure, ensuring a seamless and durable bond. Optionally, coating layers can be applied to either the fabric or film before lamination to improve adhesion, resulting in a robust, laminated fabric suitable for various applications.
Spread Coating / Knife-Over-Roll
In the spread coating or knife-over-roll process, a precise amount of coating solution is applied onto the substrate as it moves under a knife set at a specific gap above a support roller. As the fabric and coating pass through this controlled gap, any excess coating is neatly scraped off, ensuring a uniform coat on the fabric. The coated fabric then moves through an oven where the coating is set, resulting in a consistently coated product ready for use in various applications.
Immersion (Dip) Coating
Our immersion coating process involves submerging the substrate into a bath containing a low viscosity polymer solution. Post-dipping, the substrate passes through pressure rolls. This step ensures any excess coating is effectively removed and recirculated back into the dip solution. The result is a uniformly coated fabric, ready for further processing or application.
Hot Melt Coating & Lamination
Our hot melt coating and lamination process utilizes high temperatures to apply a solvent-free adhesive to the substrate, offering an eco-friendly solution without the need for drying or curing time. The amount of adhesive is meticulously controlled by an engraved rotogravure roller, ensuring consistent application. Following the coating, a second substrate can be laminated onto the first, creating a composite material with enhanced characteristics, suitable for various applications and ensuring a strong, reliable bond.
Transfer Coating
The transfer coating process is an advanced method for applying multiple layers of coatings to a substrate. Initially, a roll of casting paper is unwound and passed through stages where different polymer coatings - known as topcoat, intercoat, and tiecoat—are applied. Each coated layer is dried in an oven to ensure proper adhesion and curing. Following the application of the tiecoat, the fabric is unwound and laminated onto the coated paper. The composite then goes through another oven to bond the coatings to the fabric. The fabric is separated from the paper and rewound. Finally, the paper is rewound for reuse. This results in a fabric with a high-quality finish and handle, tailored for specific performance requirements.
Reference https://www.trelleborg.com/en/engineered-coated-fabrics/solutions/processes